前回に引き続き今回も「モノづくり」の基本です。
ミス防止と現場の3大ムダとは?
ミス防止について「5M1E」の変化に注目
仕事のミスはへこみます
そんなミス防止には[5M1E」の変化に注目せよ!
- Man(人間)…人の顔色・機嫌の変化など
- Machine(機械)…機械コンディションの変化など
- Material(材料)…質の変化など
- Method(やり方)…従来と異なるやり方ではないか?など
- Major(目盛)…異常値ではないか?など
- Environment(環境)…寒暖や明暗、その他環境の変化など
つまりこの6項目(人・機械・材料・やり方・目盛・環境)の変化に気付けるかがミス防止につながるということです。
なるほどな~っと思いましたが、ミスはやはり「ゼロ」にはなかなかならないですよね、同じミスを繰り返さないことが大事だと思います
ですが、失敗を恐れて何もできなくなってしまったり、実力を出し切れないのも困ります
「失敗は成功の元」
失敗は成功までの過程です、過度に恐れずに何事も挑戦していきたいです。
挑戦すると言えば「セルフハンディキャッピング」という心理効果があります、誰にでも1度はあると思います。
無意識のうちに失敗を恐れて、失敗の理由を作ってしまうこと。その結果が良くても悪くても自尊心を守ろうとする。
試験前日に部屋の掃除したくなるなどのやるべきことが決まっているのにそれを妨げる行動を起こしてしまう。そして試験の結果が悪かったとしても「掃除してたから結果が悪かった」、逆に良かった場合でも「掃除してたけど結果は良かった」とどちらにしても自尊心を傷つけずに済む。
この効果の怖いところは「無意識」なところです。なのでこういった心理効果があるんだ、ということだけでも心の隅に置いていただき気付きとなり、あなたの挑戦の妨げを防止することができれば幸いです
現場の3大ムダとは
仕事していて「無駄だなあ」と思うことは、私でも多々あります。物が散乱している現場であったり、必要以上に在庫があったりする「物」のムダもあるのですが、何と言っても「時間」のムダこれがとても目につきます。
今回の受けた研修では、「3大ムダ」として山田日登志氏の考えについてのお話でした。
- 停滞…流れが止まる
- 運搬…移動のムダ
- 動作…時間のムダ
…むむっ?結局3つとも全部時間のムダじゃない?
もう少し自分なりに深堀してみたところ「トヨタ生産方式」のなかでは「7つのムダ」を徹底的になくすようにしているそうです。その7つとは、
- 作りすぎのムダ
- 手持ちのムダ
…材料が足りないなどで作業が始められない「手持ち」ということ - 運搬のムダ
- 加工そのもののムダ
- 在庫のムダ
- 動作のムダ
- 不良を作るムダ
分かりやすい。そして最初の3つとも被っていますね、「手持ちのムダ」は「停滞」と同意になると思います。
言い方は色々とありますがやはり「時間」をムダにしないということが重要なのかなと私は感じました。常日頃から「時間は平等で有限」を意識しているからかもしれませんが、やはりムダな事には時間を使いたくはないですね。
企業に属して仕事していること自体が自分の人生の貴重な時間を切り売りしているようなものですから定時内でしっかり働いて、しっかり稼いで残りの時間はプライベートを充実させたい
次はその「ムダ取りの基本」についてです。
ムダ取りの基本
ムダ取りの基本については大きく4つのことができます。
- 廃止…やめる
- 削減…減らす
- 標準化…統一
- 機械化…効率化(自動化)
標準化について
標準化については、具体的には
「誰もが同じように作業し、同じ品質でできるようにSOP(標準作業手順書)を作成する」
今ゆる「マニュアル」や「手順書」と言われるものの作成です
あなたの会社にそういった書類はありますか?残念ながら私の会社にはありません。入社当時、私もすぐに聞きました。入ってくる新人さんにもよく聞かれます。でもないものは無い!
自分の備忘録として、メモしたり、写真を撮ったりはしていますがマニュアルというにはほど遠く、今後の大きな課題の一つです。
見て、聞いて、やって覚えるしかない!
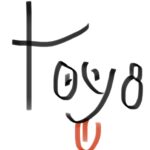
時代は令和、会社は昭和
OJTとは
「うちはOJTでやってます」なんてかっこいいこと言ってますが、実際はそんないいものではない。ざんねーん!
On the Job Trainingを略してOJT。
職場内訓練と言われ、日常業務をこなしながら、技術・スキルを身に着けていく。その指導者は先輩や上司で行うことが多い。
アルファベットで言うたら聞こえはいいけど、結局は現場に放り投げ。
このやり方は人によっても、業種、職種によっても向き不向きがあると思います。私自身は人と話すのが苦手ではなかったのと、結婚直前で転職していたので必死だったこともありなんとかここまで来ました。気難しい職人気質の先輩たちに、愛想笑いで教えを乞うのは本当に苦労しました。
標準化にはSOPが効果的
少し話はそれましたが、作業のムダを省く「標準化にはSOP作成が効果的」ただしその作成には必要作業の洗い出しから、品質の均一化に至るまでかなりの時間が必要となります。
まとめ
2回に分けて「モノづくりの基本」について、その②は「ミス防止とムダ」についてでした。
ミスもムダも「ゼロ」にするのは、難しいと思います。でも減らすことは絶対に出来る!
そして基本は大事だなと改めて思いました。
あなたが仕事をする上で何か一つでも参考になれば幸いです、ありがとうございました!
コメント